How Packaging Machine Repair Can Help You Avoid Unexpected Downtime
How Packaging Machine Repair Can Help You Avoid Unexpected Downtime
Blog Article
Extend the Life of Your Product Packaging Equipment With Professional Repair Work
In today's affordable landscape, the longevity and efficiency of packaging equipment are critical for keeping functional excellence. Involving expert repair service solutions not just addresses immediate mechanical and electrical issues but additionally fosters a society of routine maintenance that can substantially improve equipment efficiency. With proficient service technicians equipped to use top notch components that align with supplier requirements, companies can alleviate downtime and decrease functional prices. Nonetheless, recognizing the full range of benefits and the ideal technique to selecting a repair work solution can be critical, bring about an extra calculated financial investment in your machinery. What should companies consider next?
Importance of Normal Upkeep
In the realm of product packaging devices, the relevance of normal maintenance can not be overemphasized. Regular upkeep guarantees that machinery runs effectively, reducing the possibility of unexpected breakdowns that can interrupt manufacturing schedules. Normal maintenance includes methodical examinations, cleansing, lubrication, and modifications that are vital for ideal efficiency.
In addition, upkeep offers as a proactive strategy to determining possible problems before they intensify right into pricey repair services. By dealing with small deterioration immediately, services can extend the life expectancy of their tools, protecting their resources investments. This preventive technique not only minimizes downtime but likewise improves overall performance.
Furthermore, routine upkeep plays a critical duty in ensuring conformity with safety standards and laws. Well-kept equipment is much less likely to present safety dangers to operators, thereby promoting a much safer working setting. It additionally helps in keeping item high quality, as correctly functioning tools is important in adhering to specifications and lessening issues during the packaging procedure.
Advantages of Expert Repair Service
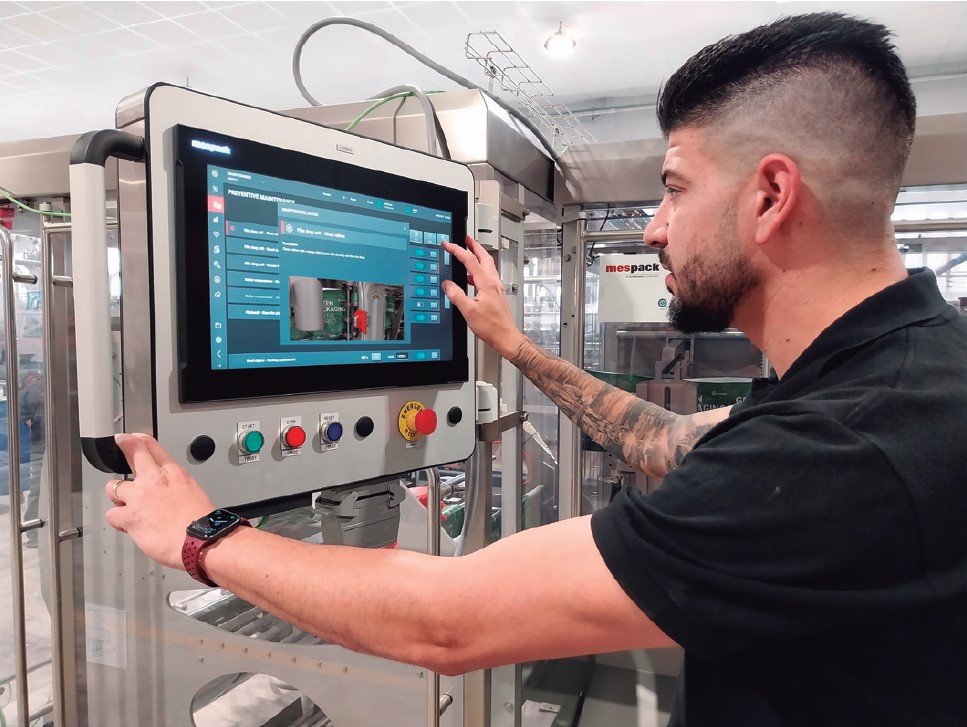
Additionally, expert repair services frequently make use of top quality components and products that surpass or fulfill producer requirements. This dedication to quality makes certain that the repaired equipment runs at optimal performance degrees, prolonging its lifespan and reducing the probability of future malfunctions.
Additionally, specialist repair can cause expense savings in time (packaging machine repair). By resolving issues without delay and successfully, businesses can stay clear of the high prices connected with complete tools replacements. Regular specialist maintenance can maximize the efficiency of product packaging equipments, leading to enhanced efficiency and, consequently, greater earnings.
Finally, depending on specialists for repair services promotes conformity with market criteria and security policies, mitigating risks connected with improper handling of devices. Basically, buying expert repair service solutions not only suffers equipment performance however also adds to a much more efficient, risk-free, and successful functional setting.
Usual Packaging Equipment Issues
Comprehending usual product packaging tools problems is vital for maintaining operational efficiency. Product packaging equipment typically faces an array of issues that can interrupt production and compromise item stability. One widespread concern is mechanical failure, which can originate from damaged parts, misalignment, or absence of lubrication. Such failures may result in unexpected downtime and expensive repair work (packaging machine repair).
Another typical problem is electric malfunctions. These can result from faulty wiring, blown merges, or outdated control systems. Electric troubles can cause devices to operate erratically or stop working to begin entirely, impacting the entire packaging line.
Furthermore, product jams regularly happen due to incorrect arrangement, particles accumulation, or used components. Jams not just halt manufacturing yet might also harm the products being refined, causing more losses.
In addition, inconsistent labeling or securing can emerge from equipment wear or incorrect calibration, weakening item high quality and compliance with sector requirements. Last but not least, poor upkeep practices typically add to a decrease in equipment performance, making normal examinations and servicing vital. By acknowledging and resolving these common problems, firms can enhance their packaging operations and extend the life expectancy of their tools.
Picking the Right Repair Service Solution
Picking the appropriate fixing service for packaging devices is important to minimizing downtime and making sure functional effectiveness. When reviewing prospective company, consider their know-how and field of expertise in the kind of equipment you make use of. A company with a proven performance history in your particular machinery will likely offer even more trusted and effective repair services.
In addition, examine the qualifications and certifications of the professionals. Knowledgeable professionals that are skilled in industry standards can determine issues faster and implement solutions extra properly. Researching client reviews and testimonies Going Here can additionally give understanding into the provider's reputation and reliability.
An additional important aspect is the schedule of emergency situation assistance. Tools failures can happen unexpectedly, and having access to a responsive repair solution can considerably reduce the influence of downtime. Make inquiries regarding the warranty used on repair work, as this can reflect the self-confidence the solution copyright has in their work.
Finally, consider the interaction and support framework of the repair service. A company that prioritizes customer support will not only keep you informed throughout the repair service procedure however will additionally be most likely to use continuous maintenance referrals to extend the life of your devices.
Price Savings Through Expert Fixings
Just how can spending in expert repair services cause significant expense financial savings for your product packaging devices? Involving skilled technicians for repair services guarantees that concerns are precisely detected and successfully resolved, protecting against additional damage and costly downtime. Expert repair solutions use specialized expertise and tools, which can lead to extra effective maintenance than internal efforts, consequently minimizing labor expenses.
Moreover, timely fixings can extend the life expectancy of your tools, delaying the demand for pricey replacements. By preserving optimal functioning, you additionally boost manufacturing effectiveness, which equates to reduce functional costs. When devices run efficiently, there is much less waste, and efficiency degrees continue to be high, enabling for much better earnings margins.
In try here addition, professional repair work frequently come with assurances or guarantees, supplying assurance and monetary defense against future failures. This assurance can reduce unanticipated expenditures and assist in much better budgeting for upkeep.
Lastly, purchasing expert repair service services promotes a proactive technique to equipment administration, promoting a culture of normal upkeep checks. This method better boosts total devices reliability, inevitably leading to sustained price savings over time. Focusing on expert repair work is therefore a smart economic choice for services reliant on product packaging equipment.
Verdict

Engaging professional repair solutions not only addresses instant mechanical and electrical problems yet likewise cultivates a society of regular upkeep that can dramatically improve equipment performance.Professional repair service of product packaging tools offers countless advantages that can significantly improve functional effectiveness.Exactly how can investing in specialist repair work lead to substantial price financial savings for your packaging tools? Focusing on specialist repairs is therefore an intelligent monetary choice for businesses reliant on product packaging devices.
In final thought, the long life and effectiveness of product packaging equipment can be considerably boosted with normal upkeep and professional repair service services.
Report this page